Growing campus meets thermal energy needs without new power production
Growing campus meets thermal energy needs without new power production
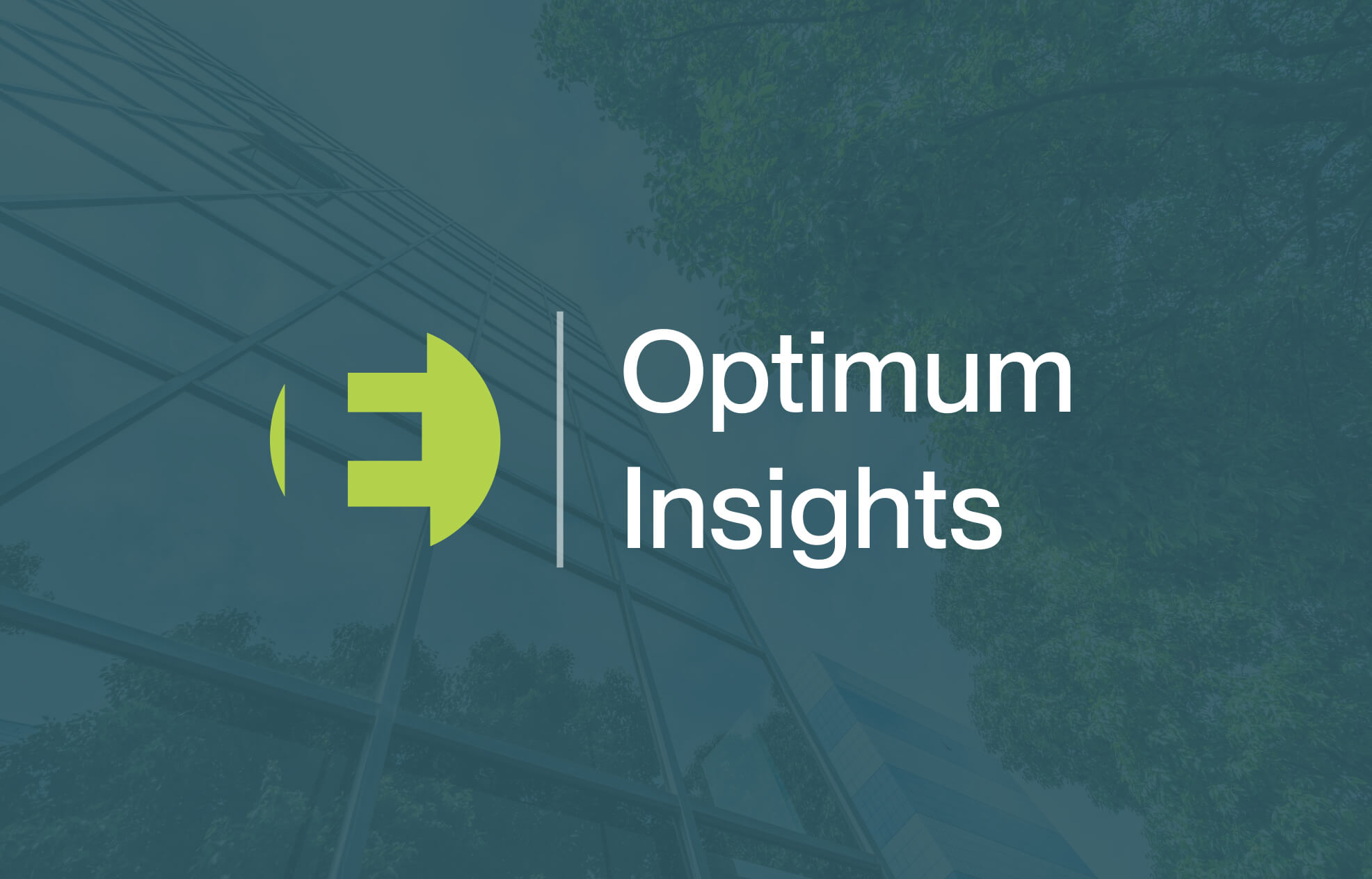
An enduring partnership enables UT Austin to deliver innovation, efficiency and energy savings.
This article originally appeared in Districted Energy Magazine
Juan Ontiveros, PE, Associate Vice President for Utilities and Energy Management, The University of Texas at Austin; and Ben Erpelding, PE, Chief Technology Officer, Optimum Energy
In 2007, The University of Texas at Austin (UT) was on the brink of massive change. With the campus expanding and its cooling systems at capacity, UT’s energy management team built a new chiller plant – and then took a chance on cutting-edge optimization software, betting that it would help keep costs down and conserve resources. It was the first step in what turned into a 13-year journey to implement increasingly complex and innovative energy efficiency measures across a steadily growing campus.
The initial chiller plant optimization project led to an ongoing engineering partnership between the UT Utilities and Energy Management (UEM) team and Optimum Energy that is reducing costs by $15 million a year and has turned the university into one of the world’s most efficient utilities.
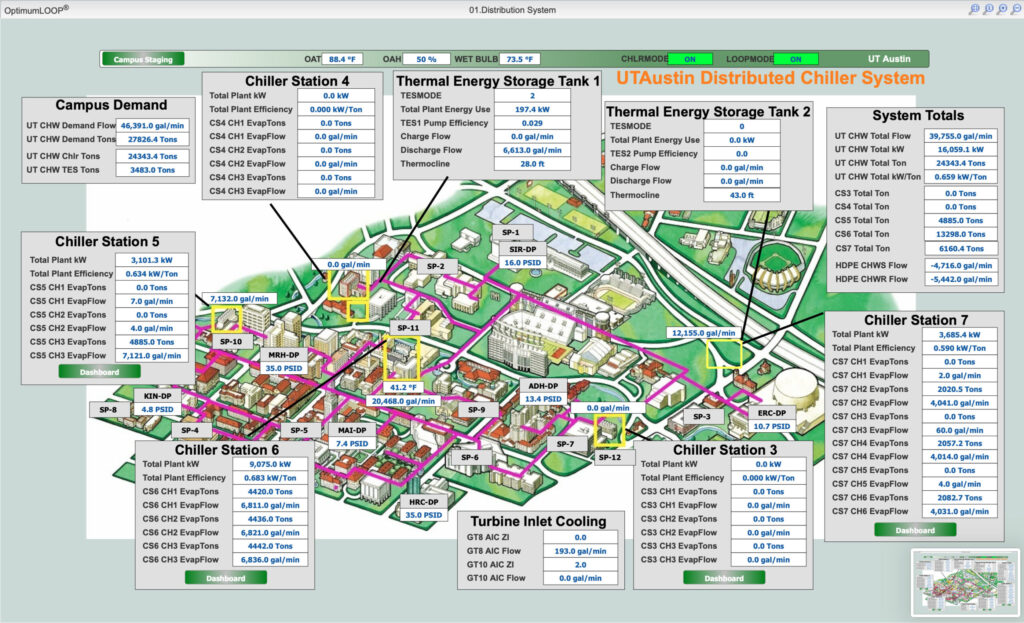
is happening and allows it to immediately see and address issues.
By combining efficiency measures with two thermal energy storage (TES) systems, UT is managing load growth, saving money and energy, and supporting the university’s sustainability goals. It has managed to reduce the chilled-water system’s overall energy usage and avoid investing in new power production capacity – even as the campus has grown by over 30 percent.
The UT and Optimum teams’ collaboration and methodical – almost religious – approach to gathering accurate data have allowed them to stretch the boundaries of what’s possible with optimization, building on each successful incremental change until, in 2019, UT achieved an average efficiency of 89 percent for all systems.
Read full article here