Optimum Energy awarded Ecovadis Bronze Medal for 2020 Sustainability
Optimum Energy awarded Ecovadis Bronze Medal for 2020 Sustainability
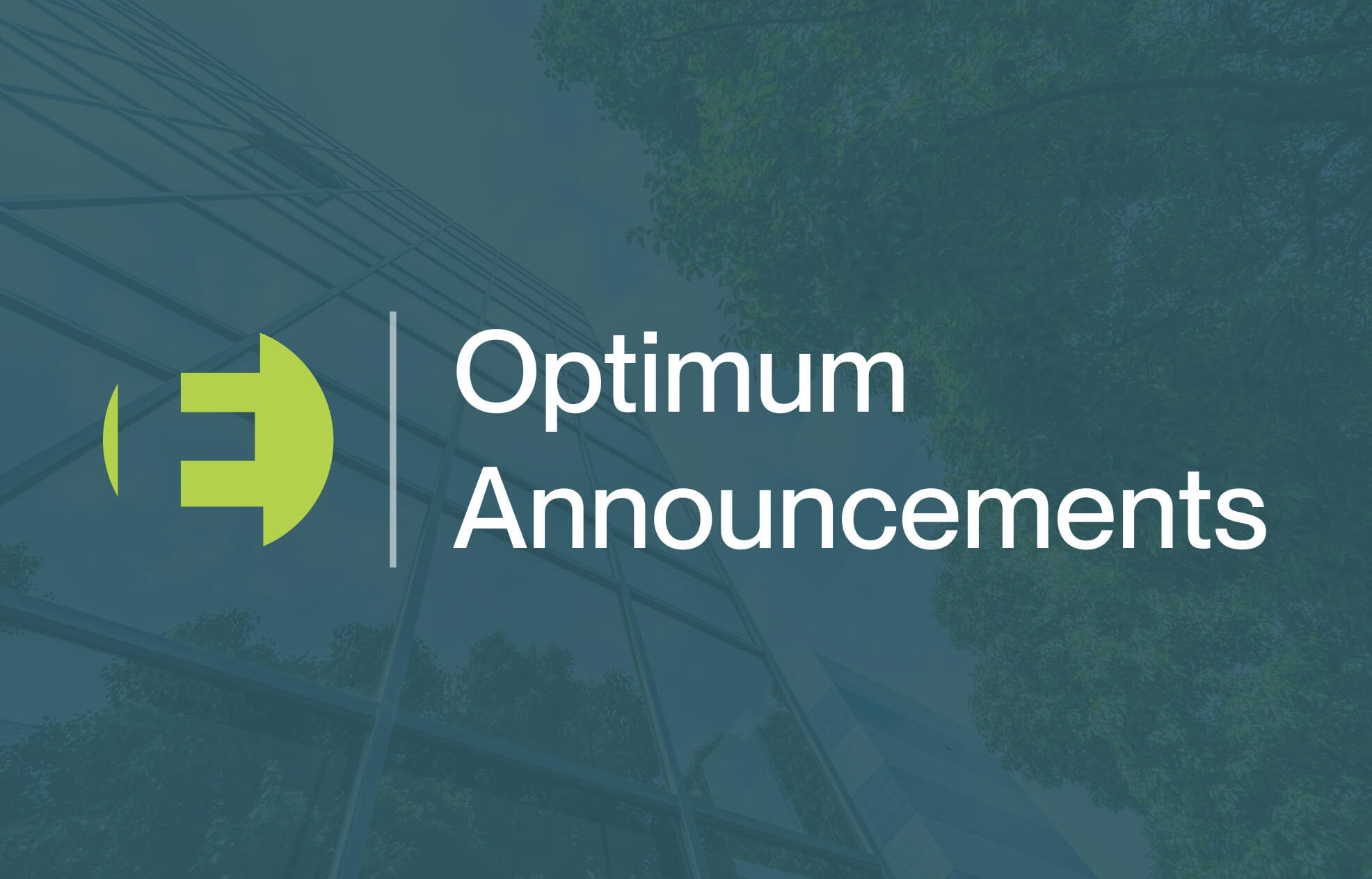
Optimum Energy is proud to announce that Ecovadis, the leader in business sustainability ratings, has awarded us their Bronze Medal 2020 Sustainability rating, placing us in the top 50% of companies they assessed. The sustainability rating is a testament to our focus on ethical and sustainable business practices. It’s also confirmation that at Optimum Energy we don’t just help our customers meet their sustainability goals, we practice what we preach. For more information on Optimum Energy’s mission and the values that drive us, visit our About page. And to see how we are helping our customers reach their sustainability goals, visit here, or check out the savings counter on our main page.