TECO: A deep dive into optimization data yields unexpected savings
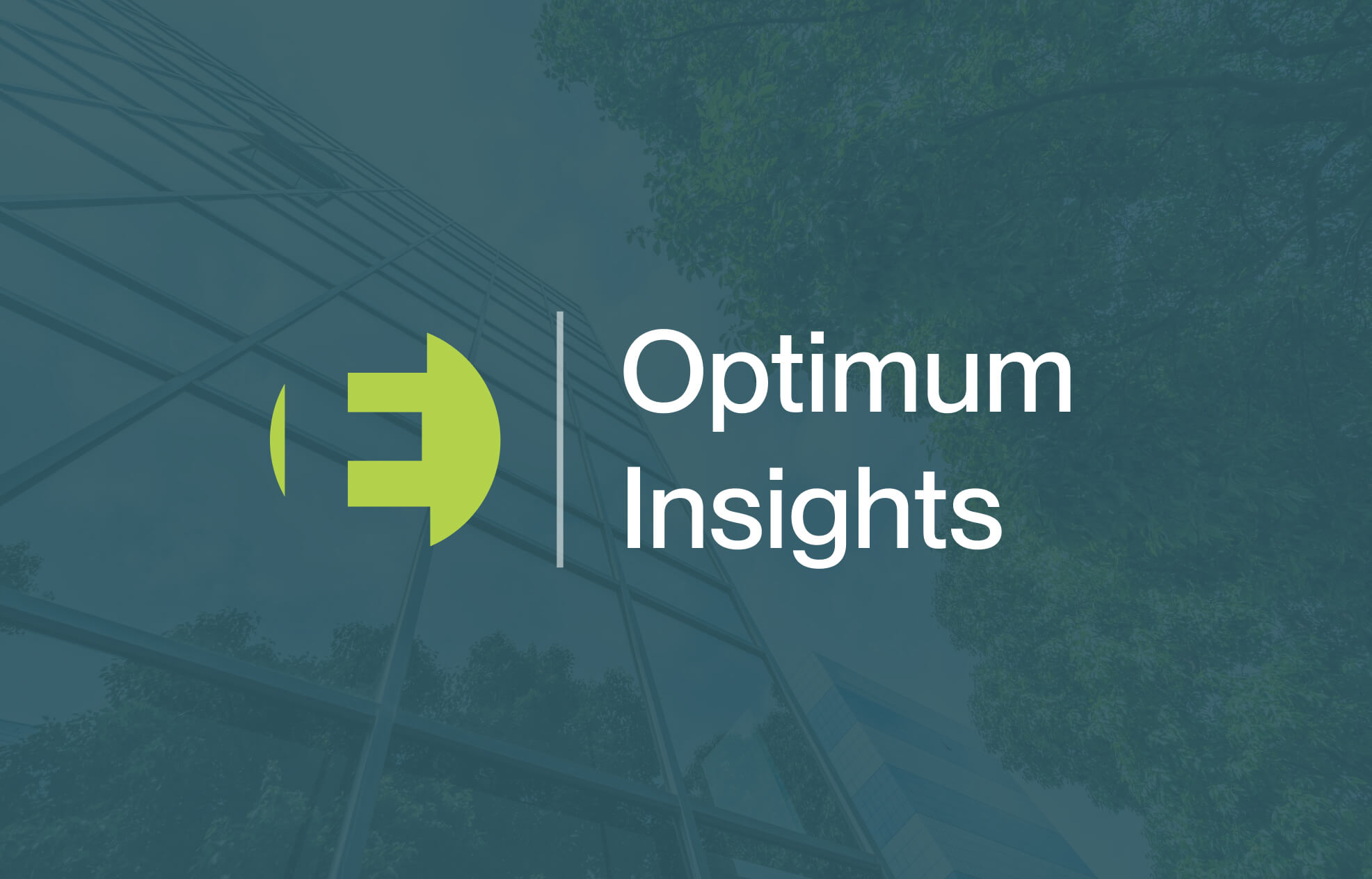
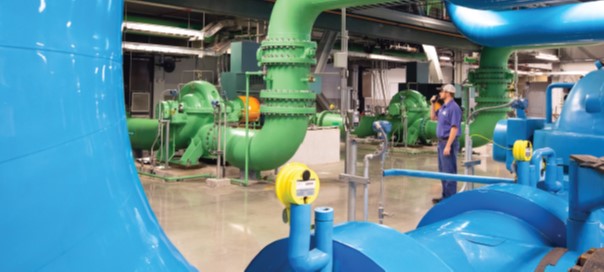
Layered efficiencies drive down costs while maintaining reliability
This article originally appeared in Districted Energy Magazine
Michael P. Manoucheri, P.E. is TECO’s president and CEO; and Ben Erpelding, PE, Chief Technology Officer, Optimum Energy
A three-phase initiative to explore and implement cost savings across the largest district cooling system in North America has paid off handsomely and quickly bringing significant system improvements even in the midst of the COVID-19 pandemic. Efficiency gains have been seen in condenser management, chiller operations, and thermal energy storage.
The project’s genesis can be traced to IDEA’s annual conference in June 2019, when representatives from Thermal Energy Corporation (TECO) and Optimum Energy struck up a conversation about the pitfalls of drawing electricity from the grid in the sweltering heat of a Texas summer.
The TECO team wondered if the company could decrease electrical consumption from its main site before June 2020, the start of the next peak demand season. Customer chilled water demand was growing rapidly enough to soon exceed on-site generation resources.
TECO needed a solution that would maintain reliability, keep costs down and conserve resources. That initial conversation, in 2019, turned into a multiphase, plant-wide optimization journey that now saves TECO $550,000 and 16.1 million kWh of energy annually – even as customer demand for chilled water continues to rise.
TECO, named IDEA’s System of the Year in 2019, provides chilled water and steam to Texas Medical Center in Houston, which – as the world’s largest medical campus – requires reliable, economical heating and cooling and has growing needs.
Peak chilled water demand has increased by 9,000 tons over the past four years and is expected to grow by an additional 9,000 tons over the next three years. TECO has found that the most cost-effective way to manage district growth while maintaining its historical reliability of 100%, with no unplanned outages since 1992, is to layer on new efficiency measures.
Partnering with Optimum Energy, TECO’s engineering team developed a three-phase plan. First, for the condenser water system to conserve more energy and reduce costs; second, to have the chiller staging procedures better handle changing loads; and third, to take advantage of real-time electricity pricing for the thermal energy storage (TES) tank dispatch.
Two years down the road, TECO has improved control over the energy balance of its CHP system and its TES tank, reducing the chiller plant’s electrical demand. In the first seven months of optimization – from June to December 2020 – TECO lowered peak demand by 2 MW, saving nearly 10.5 million kWh, and reducing the plant’s energy consumption by 6%. Now, TECO can avoid spot-purchasing power from the sometimes unreliable public grid and more easily keep up with customer demand. By reducing peak demand, TECO also bought time to develop a new master plan, including how and when to add power production capacity.
Read the full article here