Optimum’s Jesse Ohm Awarded Pump Management Patent: The Next Step for Large-Scale Fluid Pumping Automation
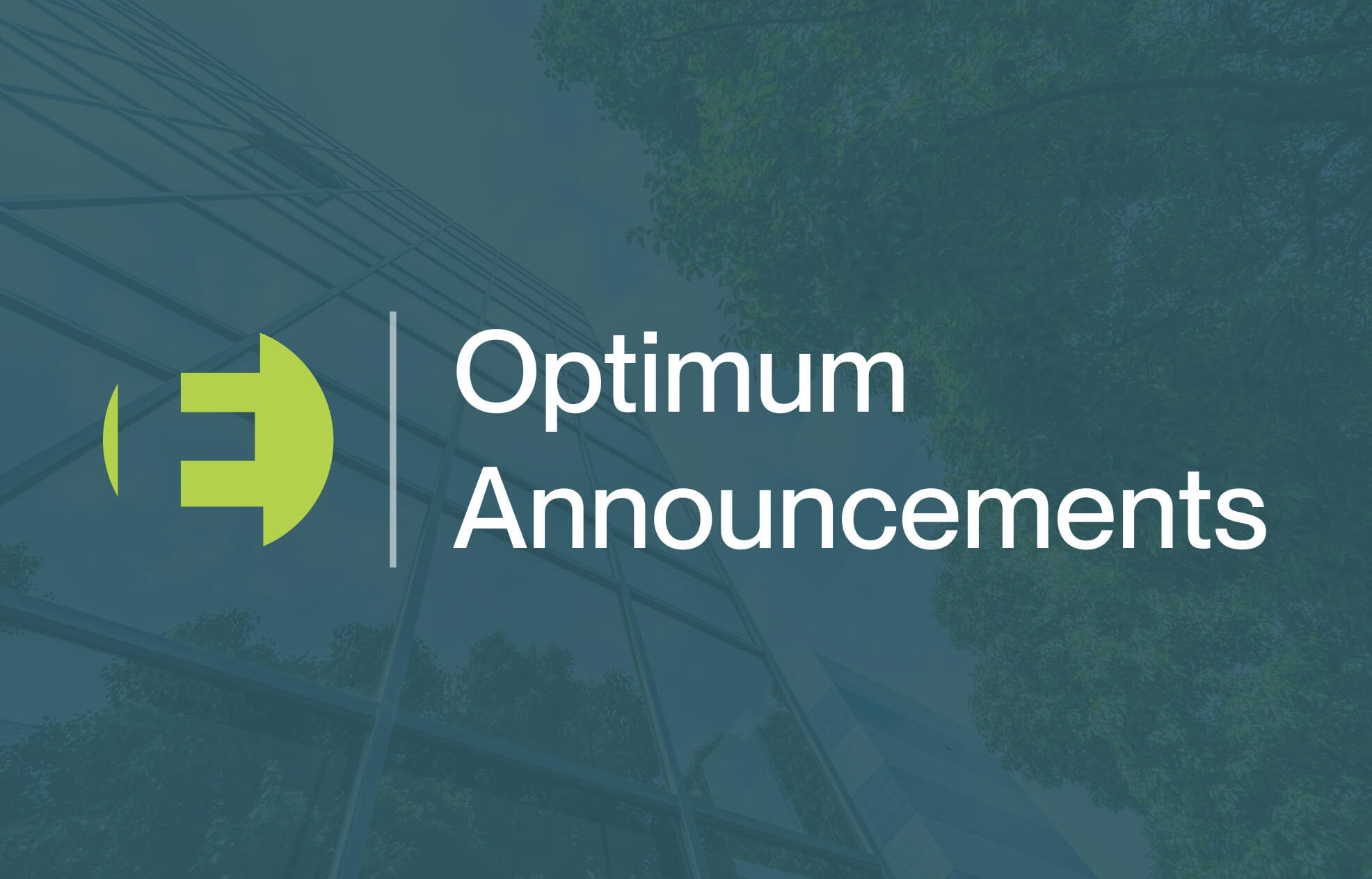
Introduction
Jesse Ohm, P.E., Principal Engineer at Optimum Energy has been awarded a patent for his new system centered on the optimization of multiple pumps using advanced computational techniques. This innovative solution has the potential to drastically improve the process in which commercial and other large-scale facilities manage their fluid flow distribution systems, while gaining an increase in energy efficiency, cost savings, and overall system performance.
Patent Overview
The newly awarded patent outlines Ohm’s method for optimizing pump staging through a computer-readable medium containing instructions executed by an automation system.
“It became apparent after observing conventional control systems that the industry needed a simple and repeatable way to calculate when to stage pumps up and down,” said Ohm. “The goal was to create a universal calculation that remained applicable under any operating conditions.” The method encompasses several key components:
Peak-Efficiency Range Determination
An automation system enhanced with the pump staging algorithms automatically identifies the peak-efficiency operating range for the pumping system. Defining the stage limits based on real-time data allows any automation system to optimize the system’s pump staging control.
Real-Time Dynamic Calculation
Continuous monitoring of the fluid-flow rate and pump speeds allows for real-time optimized stage calculations. When the fluid-flow rate drops below the algorithm’s dynamic stage-down threshold, a pump is deactivated. Conversely, if the fluid-flow rate exceeds the stage-up threshold, an additional pump is activated automatically. Since the thresholds are dynamic and based on live data, the ideal staging is continuously evaluated and works under any operating conditions.
Threshold Calculations
Thresholds for stage-up and stage-down operations are continuously recalculated from live data, based on the following inputs:
- A reference design fluid-flow rate at the manufacturer’s full speed peak efficiency point also known as the “Best Efficiency Point”.
- The live system flow rate.
- The active number of operating pumps.
- The current operating speed of the pumps.
Additional Features
- The peak-efficiency range and thresholds only require a single user data input (the pump’s best-efficiency point) making it easy to calibrate for each application.
- Stage thresholds are automatically calculated based on live operating conditions.
- The inputs do not require maintenance or recalibration unless physical changes are made to the pumping equipment.
- Equipment staging events can be limited through an automation system to any specific use case to control frequency of pump staging.
Why This Patent Matters
Energy Efficiency, Cost Savings, and Sustainability
Reduced Energy Consumption: The system activates or deactivates pumps based on real-time demand, ensuring the lowest energy use. Energy savings translate directly into reduced utility bills fewer greenhouse gas emissions, supporting environmentally friendly operations and net-zero goals.
Maintenance Cost Reduction: Maintaining pumps within their peak efficiency range can significantly reduce energy usage and decrease wear and tear, extending pump lifespan and reducing costly maintenance and downtime.
Resource Conservation: Efficient resource use aligns with sustainable practices and corporate social responsibility goals for the ESG-minded.
Improved Performance
Consistent Fluid Flow: By maintaining the pumping system in the peak efficiency operating range, the system maintains a stable and consistent fluid flow rate and pressure, crucial for processes that require precise fluid management at various pressure requirements.
Adaptability to Demand Fluctuations: The system efficiently manages varying demand levels, suitable for applications with fluctuating fluid flow and operating pressure requirements. Systems that leverage a wide range of operating pressure requirements (such as systems with pressure re-set strategies) will gain even greater advantage from the dynamic thresholds since the live data inputs automatically compensates for changes in operating pressure.
Responsiveness and Flexibility: Dynamic adjustments allow the system to swiftly respond to changes in both flow and pressure, boosting overall performance and reliability. This approach can be scaled to different sizes and types of pumping systems, offering flexibility for diverse applications, regardless of scope or industry.
Conclusion
Ohm’s method for dynamically managing pump operations represents a significant advancement in fluid flow management for large-scale facilities. By leveraging real-time data and advanced computational techniques, this system offers unmatched benefits in energy efficiency, cost savings, performance, sustainability impact, and operational flexibility. This innovation has the potential to set new standards in sustainable and efficient pump management. Industries and facilities reliant on large-scale fluid operations should consider this solution when evaluating their best course of action in the pursuit of financial, operation and sustainability-focused goals.