Cloud-Connected HVAC Systems Are at the Core of Smart Facilities
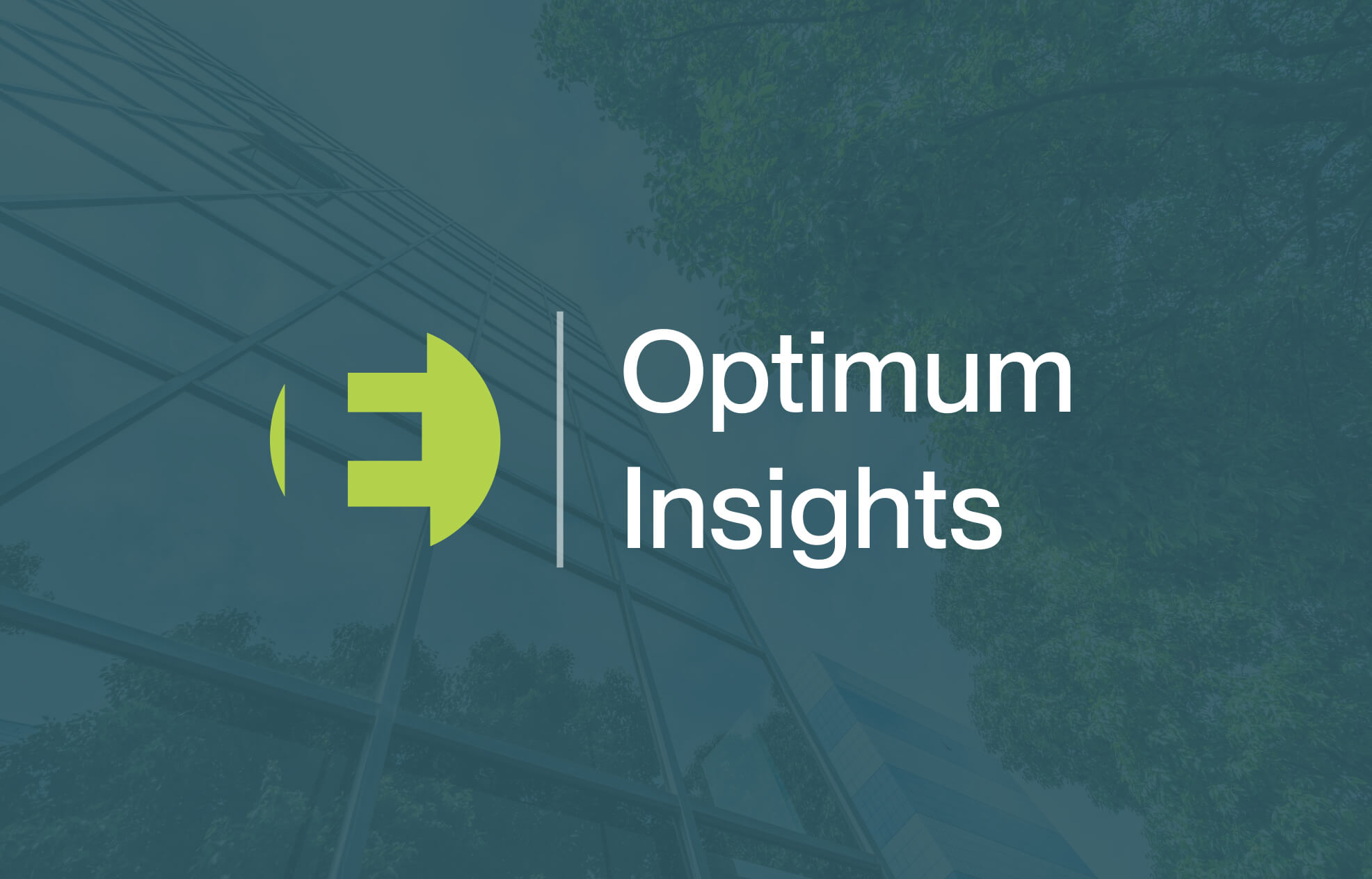
By Ian Dempster
You can’t have a smart facility without a connected HVAC system.
Facilities become intelligent only to the extent that their operators collect, analyze, and learn from the massive amounts of information flowing from building systems and equipment. HVAC data is fundamental, given that the system typically accounts for 44 percent of a commercial building’s energy consumption and is central to occupant comfort and, for many manufacturers, product quality. And that makes connecting the HVAC system to a cloud-based data center a crucial aspect of creating a smart facility.
Simply optimizing an HVAC system can yield substantial savings, reducing its energy usage and resulting costs by 20 to 50 percent (30 percent is typical). But without ongoing monitoring, those results will start to degrade after about a year or so. A two-way data flow between a facility’s HVAC equipment and building automation system (BAS) and an optimization provider’s network operations center enables real-time monitoring, analysis, maintenance, and fine-tuning of the HVAC system. It’s the only way to maintain the efficiencies gained through an HVAC system upgrade, and to gain ongoing insights into a facility’s performance.
Unconnected Systems Lose Their Edge
In the first year after optimization, results may remain constant without cloud connectivity. By the second year, typically, equipment begins to age and the facilities team probably has changed settings in the BAS, causing savings to fall off. By the third year without cloud connectivity, a site can lose as much as half of its original carbon and cost savings through natural system performance degradation and operational overrides. Without the external “brain” a cloud connection provides, the falloff can go unnoticed for quite a while, costing the facility thousands of dollars.
Establishing a two-way connection between an HVAC plant and an optimization provider can be a project, but it is getting easier: new chillers, pumps, variable frequency drives (VFDs), and even smart actuators are now designed to connect with control software and upload data to the cloud, enabling ongoing monitoring and system optimization. A facilities manager can collect and share BAS and environmental management system (EMS) data, which can reveal where the facility is consuming the most energy, whether the equipment is working correctly and efficiently, and if the automation sequence is controlling the HVAC system effectively.
At the same time, the optimization provider can watch for failing components, mechanical drift, changes in ambient conditions, and other fluctuations in the HVAC system. In response, they can access the installed optimization solution, use the data to troubleshoot the equipment, improve sequencing, and adapt set points to meet environmental parameters as they change. They can also remotely install software updates that can increase efficiencies or reliability.
Security and Product Quality Take Precedence
Connecting a BAS and EMS to an optimization provider’s data center raises network security concerns for any building or facility IT team. And for facilities with strict environmental requirements—hospitals, labs, pharmaceutical manufacturing plants—ensuring precise temperature and humidity controls is paramount. Both types of challenges require careful, collaborative information systems engineering.
The first step is to implement robust security separations between networks used for BAS sensors and monitoring, and those used for business transactions. This ensures that intellectual property, financial information, and other business-related data remain siloed from operational data.
A security-conscious optimization provider will then work with the facility’s IT team to establish a site-to-site virtual private network (VPN) tunnel between single points—a secure, private connection linking designated devices—that provides strong encryption with unique keys and access controls that give the optimization provider’s engineers access only to operational data for energy management and optimization services. In addition, the optimization software should be installed with intrusion detection, secure network connectivity, and limited user permissions. For next-level security, some vendors offer a security appliance that creates the secure VPN tunnel connection between the optimization software and the vendor’s cloud servers, using standard outbound secure ports only. That avoids the need to set up a link from the company’s network.
Where the building environment affects product quality or core operations, facility managers may worry about automated controls, believing that a hands-on approach is the only way to maintain the correct operational parameters. That’s a sure way to lose the benefits of optimization and building intelligence over time, though. The vendor should work with facility operators to fine-tune optimization settings with both efficiency and environmental needs in mind, and provide training on how the optimization system works.
Getting Connectivity Right Brings Rewards
The benefits of cloud connectivity make it well worth the effort to establish the appropriate security setup. First and foremost is the assurance of continual energy-use and cost reductions. For example, we’ve seen an 18-million-square-foot university campus improve the efficiency of its chiller plants by 23 percent. Every year, the facility is saving more than $1 million due to the cloud-connected optimization software. We’ve also seen a 110,000-square-foot research laboratory improve its efficiency more than 27 percent by optimizing and connecting the chiller plant. Hershey Medical Center in Pennsylvania is saving more than $300,000 a year using connected optimization software, which reduced facility energy use by 4 GWh annually and improved system efficiency by 21 percent.
Sharing operational data via the cloud also provides greater visibility into HVAC, BAS, and EMS systems, leading to better control over the equipment. A two-way data flow enables full access to the analytics software as well as the HVAC equipment from any location. The facility manager can check on the chiller, for example, from home first thing in the morning, and the optimization vendor can remotely troubleshoot the system right down to its individual components. Even mechanical problems can get fixed much faster, because repair people know in advance what isn’t working.
Additionally, cloud connectivity allows the transfer and storage of large amounts of operational data cheaply and securely off-site.
Even Smarter Systems Are on the Horizon
Machine learning and artificial intelligence are poised to enable even better control of HVAC systems. With data sequencing, archived data, and efficiency and building energy models, optimization and analytic software can learn how various pieces of equipment respond to different conditions and can tell the BAS how to most efficiently run the HVAC system in real time, or even predict the best equipment to use in future conditions.
Automatic optimization through machine learning could increase savings—we’re already starting to see companies gain an additional 5 to 7 percent efficiency improvement through machine learning programs added onto their optimization platforms. One example is dynamic sequencing, which determines the most efficient combinations of equipment to run, taking into account system load, weather, and occupancy. The program learns over time, and as equipment efficiency changes it determines new sequences to maintain or even improve system energy savings.
Two-way connectivity through the cloud is what enables that kind of machine learning—which is ultimately what will make a facility smart.
This originally appeared in ACHR News.