How to optimize an HVAC system
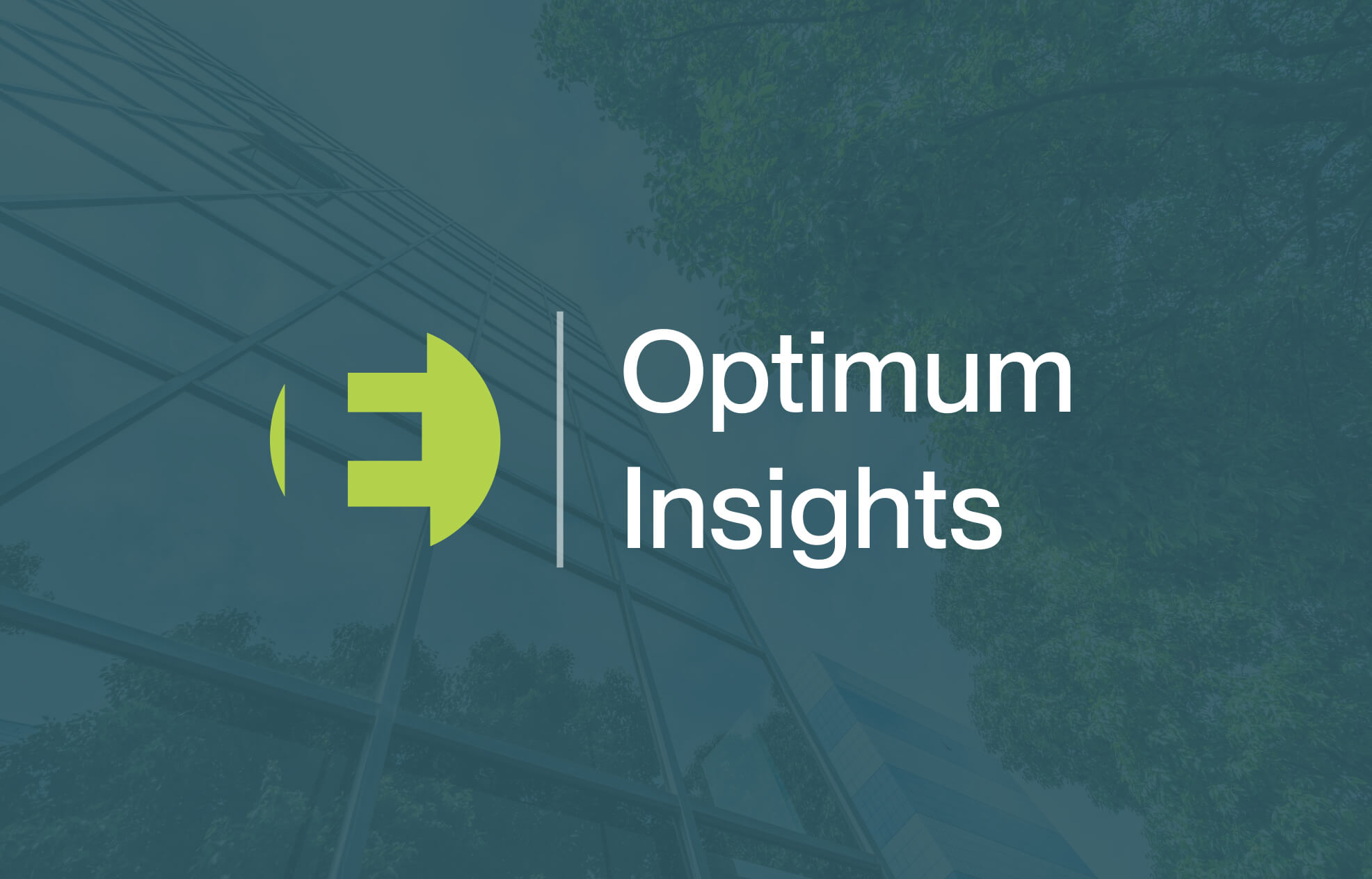
By Eric Toback, PE, LEED AP, Optimum Energy VP of Sales
When designing a high-performance building, engineers search for the most energy-saving HVAC components—super-efficient chillers, high-efficiency pumps and cooler towers, and variable frequency drives (VFDs). But even the most efficient components cannot reach aggressive energy targets on their own. Reaching peak performance requires a broader, holistic approach to efficiency that includes central plant optimization.
The trouble is, “optimization” has become a buzzword in the facilities management industry, with competing vendors offering a wide array of solutions. This creates the belief that optimization is a stand-alone bill of goods. Some vendors say the solution is a piece of hardware, some say it’s software, while others say it’s a cloud-based dashboard. But the truth is central plant optimization is not a single thing. It’s an overall methodology that starts with a good design and construction, integrates automation and optimization, and provides maintenance and monitoring throughout a building’s lifecycle. When done correctly, optimization maintains central plant operations at peak performance day after day, year after year.
Optimizing central chiller plants, specifically, is critical because they usually consume more energy than any other building system; however, the lessons also apply to airside and boiler systems.
HVAC optimization
For true optimization, the solution must automatically control HVAC equipment as a holistic system 24/7 so that it uses the least amount of energy without sacrificing performance. It’s impossible to judge a solution’s optimization capabilities without first understanding the three laws of optimization:
- Measurement comes first. Without an accurate measure of energy use by each piece of equipment, it’s impossible to accurately predict and report the impact of varying conditions on the entire system. If you can’t measure it, you can’t optimize it.
- Optimize systems, not just individual components. If an optimization plan focuses only on installing the most efficient pieces of equipment or saving energy in one subsystem without considering how to maximize the performance of the whole system, it will fail to capture the total available efficiency potential.
- Optimization must be automatic, dynamic, and continuous. To achieve maximum efficiency, optimization must be a real-time dynamic process, not a static set-and-forget process. Operational control must be automatic and based on real-time inputs and adjustments.
When optimization fails to meet expectations, it’s often because the solution couldn’t deliver closed-loop optimization in real time. Products sold as being able to “optimize” vary widely, from efficient components to component-based efficiency tools to systemwide HVAC optimization. Because no standard definition for “HVAC optimization” is guiding the industry, engineers often don’t get the energy and cost savings they expect from the products they specify.
HVAC efficiency strategies
Several efficiency strategies can reduce energy consumption, but they fall short of true optimization when they are deployed alone.
Energy-management and analytic dashboard solutions provide much-needed insight into how a plant’s various components are consuming energy, and some can even make actionable recommendations for ways to gain energy savings. This meets the requirements of the first law of optimization (measurement comes first), but it falls far short of true optimization, which automatically reacts to system conditions before the energy has been wasted.
Fault detection and diagnosis (FDD), which automatically detects and diagnoses performance faults, is an extremely valuable tool that ensures HVAC systems remain healthy in the long term. But on its own, FDD has drawbacks. FDD rules can be applied to any sensor, meter, valve, or pump in a chiller plant, with alarms notifying the operations team whenever key values drift from a specified range. However, operations teams cannot easily prioritize the FDD-armed sensors that are critical to system reliability and savings over those that are not.
Chilled- and condenser-water resets are standard practice for efficient plant operations. Chillers run more efficiently when refrigerant lift and compressor work are minimized by specifying warmer chilled-water setpoints and a colder condenser-water setpoint. Resets must be done carefully, though, with the impact on the total system’s energy consumption factored into the decision. While these component-based optimization strategies may deliver some energy savings at the chiller level, those savings may be lost if the chilled-water pumps or cooling tower fans must work harder to compensate. For example, increasing the chilled-water supply temperature decreases the log-mean temperature differential and associated heat-transfer quantity of the air handling unit’s cooling coil, which often requires more chilled-water flow and pumping energy to meet the same cooling load and humidity requirements.
In many facilities, the first—and sometimes only—optimization technique deployed is installing VFDs that use proportional-integral-derivative (PID)-based controls throughout a chiller plant. PID loops are industry-standard ways to control individual components (and should be incorporated in certain situations), but they typically focus only on individual components, thus fail to deliver systemwide benefits no matter how many are installed. They also require substantial tuning to provide smooth, stable operations. System hunting is commonwith PID-based optimization, especially when using temperature or pressure setpoints, as significant latency can occur between the time when a specific setpoint is sent and the time when a resulting change in sensor feedback is realized. This often causes enough frustration to goad operators into turning off the optimization system.
Another standard practice is retro-commissioning an HVAC system to bring a plant back to its original condition. This can lead to some one-time efficiency gains, but performance will drift again over time—until the plant’s next retro-commissioning cycle occurs, often years later.
HVAC optimization that works
True HVAC optimization calls for a three-pronged approach addressing infrastructure design, system automation and optimization, and ongoing monitoring and maintenance.
Optimization that works over time starts with thoughtful design. A plant must be built for operational flexibility, able to accommodate fluctuations in weather and occupancy, and outfitted with components designed for all operating conditions (instead of only the unlikely worst-case scenario).
With the right plant components, the stage is set for high efficiency—and there are fewer challenges that the optimization solution must overcome. Key design elements include VFDs on all of the plant’s pumps, cooling towers, and chillers; headered chilled-water pumps set in a variable primary configuration; headered condenser-water pumps with variable-flow operation; headered cooling towers with a 3:1 waterflow turndown ratio; low-flow bypass valves sized to maintain minimum chiller flow; and instrumentation that can capture data about individual chiller flows and temperatures, real-time chiller power, and chilled-water distribution flows and temperatures. The design also should allow all pumps and cooling towers to serve any chiller, providing full flexibility, and eliminate chilled-water decouplers and bypasses throughout the HVAC system—this prevents energy waste from unnecessary pumping.
On top of these highly efficient building blocks are the building automation system (BAS) and then the holistic optimization solution. Optimization requires automation—it provides reliability and consistency in plant operations that is simply not possible with even the most skilled human operators.
Ideally, the optimization solution is supervisory to the BAS. It should separate the two types of controls: optimization controls target energy reductions, and BAS controls remain focused on reliability. This type of solution allows facility managers to easily engage—or disengage—optimization methods in response to changing plant conditions with minimal operational risk.
The most advanced optimization solutions offer relational-based control algorithms that holistically determine the most efficient operation of the entire chilled-water system and continuously—at 15- to 30-second intervals—advise the BAS on precisely how to tune and optimize the plant in real time, responding to current building loads and changing ambient and occupancy conditions. Relational controls automatically optimize all of the variable-speed chiller plant components in relation to one another using real-time power consumption as an input. In contrast, traditional optimization strategies adjust plant operations against controlled setpoints, such as temperature, which is far less efficient.
Finally, achieving projected savings targets on a continuous basis requires nonstop maintenance and monitoring. Without it, the performance of an HVAC system degrades and savings are lost as components wear down and break and traditional optimization programming fails to adapt. Operations staff should be armed with tools for ongoing measurement, verification, and management that provide immediate, actionable insights, so they can detect and resolve issues as they happen. This allows the optimization solution to continue to meet energy- and cost-savings targets even as the plant ages.
For HVAC optimization to significantly save energy and money, it must be incorporated into the entire system, starting with the design process, and be rigorously monitored for real-time fine-tuning. An HVAC system that can continuously, automatically respond to changes in the environment will deliver the greatest efficiency—and push the building to its peak performance.